
ROLLER COASTER DESIGN TEAM
For the last few years, members of the Gator TPED have been hard at work designing, manufacturing, and assembling a functional scale model roller coaster to be displayed on campus. This scale model was designed using the same principles, practices, and standards with which real-life roller coasters are designed. Continue reading to learn more about the design and manufacturing process of the scale model.
CONTROLS TEAM
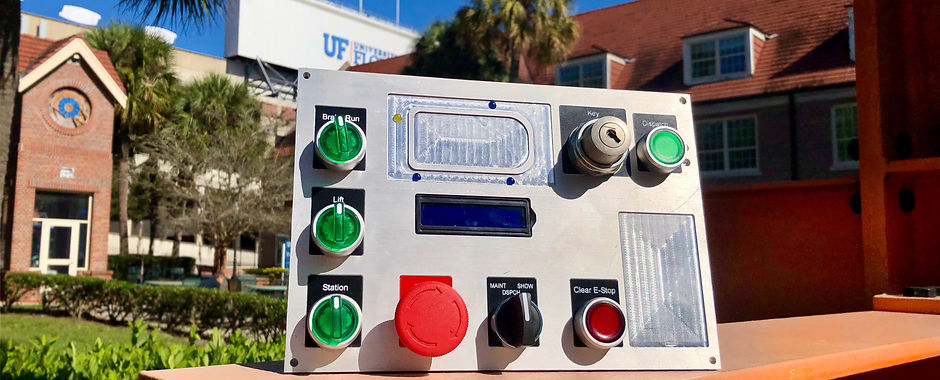
The controls subgroup of the Coaster Design Team worked to design and implement a fully functional control system for the model roller coaster. The system is able to handle the coaster with 4 different block to safely allow two trains on the track at the same time. It ensures that only one train is one the track at a time and it can only be sent down the track once the break run is clear. The system monitors sensors located at the beginning of the break run, end of break run, end of the station, and at the top of the lift hill to track the location of the train. It controls three motors to move the trains around the track, at the break run, station, and the lift hill. The motors speed and direction is controlled by a direction pin and PWM pin to control speed. The system has a fault manager to catch any time a sensor is unexpectedly triggered or the E stop button is pressed. Once a fault is detected, all trains will be stopped immediately and not able to continue until the key is inserted into the control panel and the reset button is pressed, ensuring that an authorized user has made sure that it is safe to continue operating the model. The control panel contains an LCD display that displays the status of system, including which mode it is currently in, information about the coaster’s cycle count, and error messages anytime the system faults.
MECHANICAL TEAM

The Mechanical team designed the train, lift hill, station, and brake-run subsystems. These were all fully designed in the 3D modeling software, SolidWorks and interact with a combination of gearmotors, driveshafts, wheels, chains, and sprockets. For a single cycle of the ride, the station tires propel the train through the pre-lift section of the track. The chain dog of the train then catches on the chain lift hill which is powered by a 12V gear motor that brings the train to the top. Once the train has traversed the track, the train is stopped by the brake-run tires which wait until it is clear to move the train back to the station. The majority of the mechanical subsystem pieces were manufactured using multiple 3D printers. Members of the mechanical team were also heavily involved with the manufacture of the track pieces that comprise the rest of the layout of the model roller coaster.